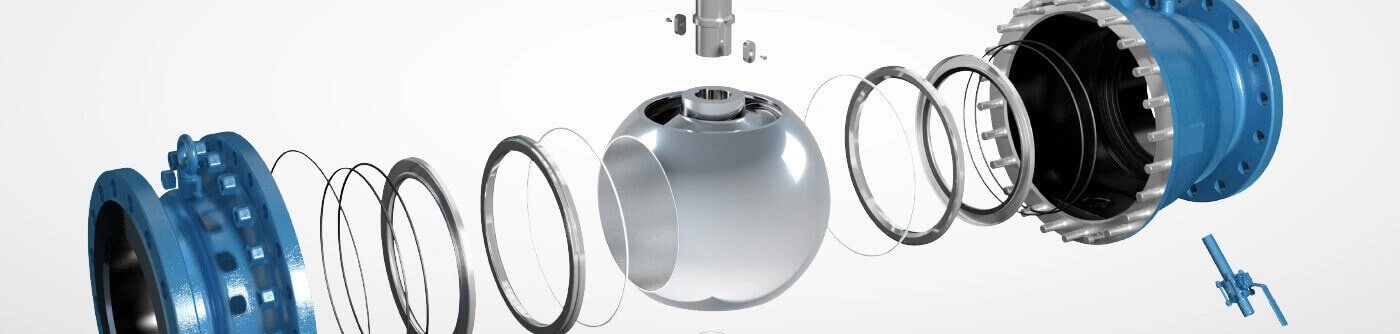
Valves
KLINGER is your partner for the development, manufacturing and worldwide distribution of industrial valves (DN 10 – DN 3000).
Our industrial valve products are “trusted. worldwide.” as a result of their high reliability, long life cycle and extremely low total cost of ownership.
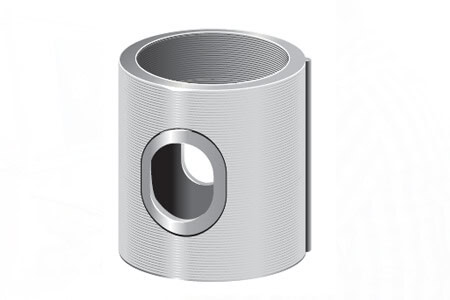
AB Cocks
Robust shut-off valves for the measurement engineering
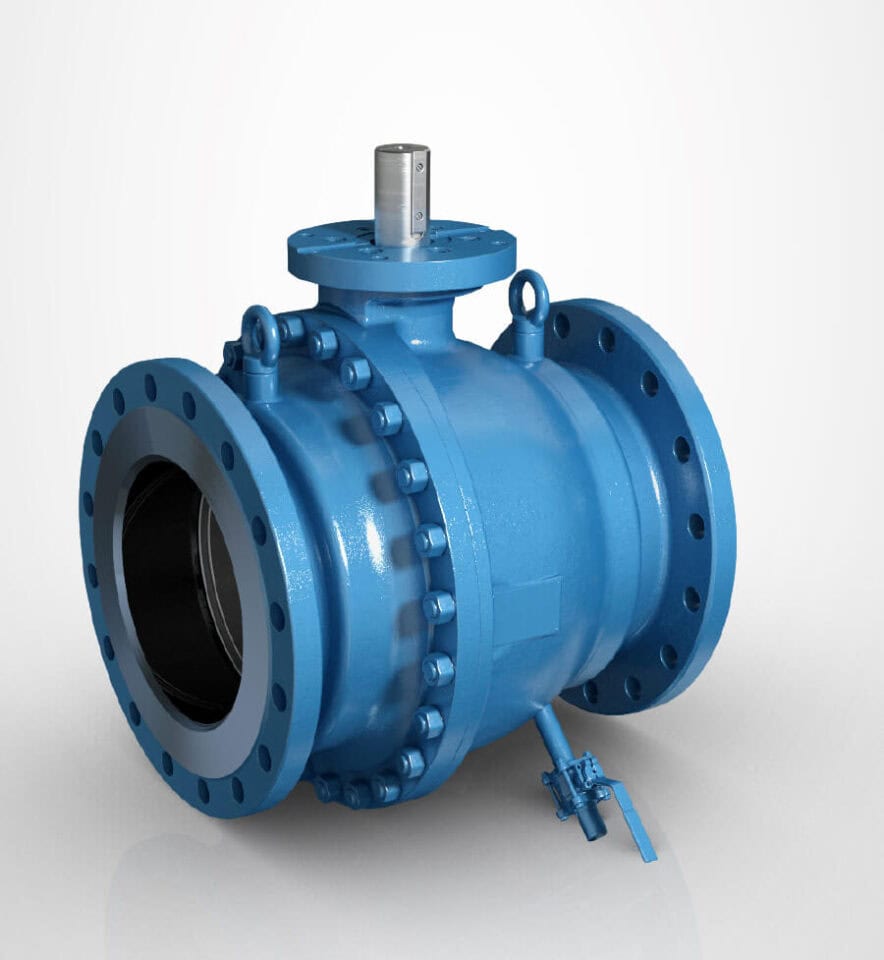
Ball Valves
Top-of-the-line valves. Ball valves are modern shut-off valves which are very reliable in operation.
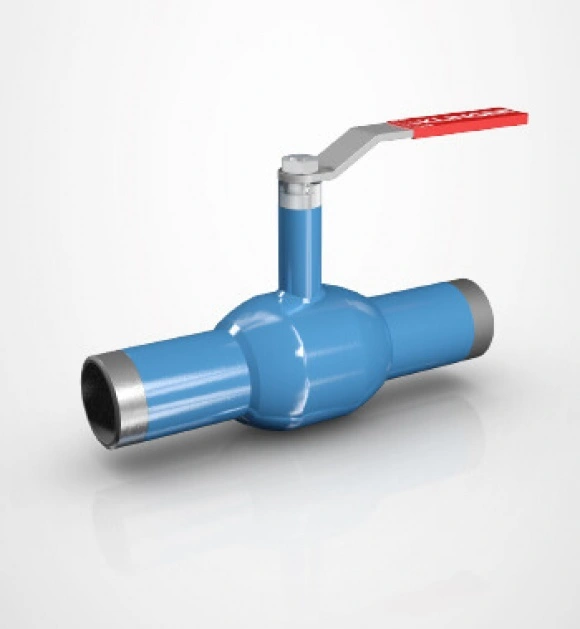
Piston Valves
KVN- The original, tried and tested a million times over